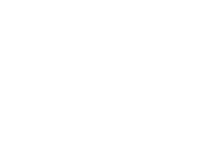
Table of Contents

Estimated read time: 18 mins
INTRODUCTION
The cost of pallet wrap in day-to-day packaging operations often goes unnoticed, yet it can significantly impact budgets when left unmanaged. In many cases, organisations focus on the cost per roll of film without fully considering how often pallets require re-wrapping, the volume of film used per load, or additional taxes that may apply. By taking a broader look at these factors, businesses can uncover the true cost of pallet wrap and adopt more efficient, sustainable practices.
Below, we’ll explore the difference between costing pallet wrap by roll versus by pallet, the role of the Plastic Packaging Tax, and how switching to a high-performance film like Shield can help reduce both costs and plastic use.
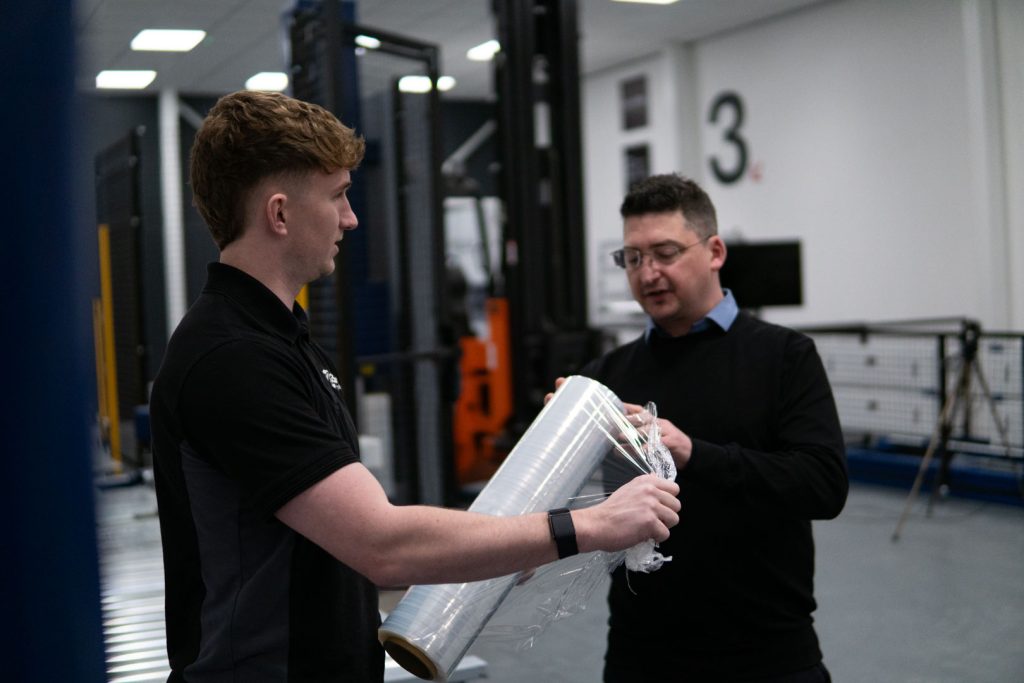
COST PER ROLL VS COST PER PALLET
The Pitfalls of Cost per Roll
Traditionally, many procurement teams base their buying decisions on the cost per roll of stretch film. At first glance, this approach may seem transparent and cost-effective. However, a cheaper film on a per-roll basis often comes with drawbacks:
Increased Risk of Breaks and Tears Low-quality films are more prone to tearing, which leads to frequent stoppages and re-wrapping.
Higher Overall Usage Because it is not as strong or stretchable, operators may compensate by using extra wraps. This adds up in both film use and labour hours.
False Economy A lower price tag per roll can mislead buyers into underestimating the total spend. Each pallet may require multiple wraps to achieve acceptable load stability, negating any savings from buying cheap film in the first place.
Why Cost per Pallet Provides Clarity
Instead of focusing on how many rolls of film are used, a more practical approach is to calculate the cost per pallet wrapped. This shifts attention to total consumption and load stability, clarifying the real expense. If you find your cost per pallet exceeds 50p on a standard load, there is a strong indication that switching to a higher-quality film could deliver substantial savings.
When the focus is on cost per pallet rather than cost per roll, procurement teams can more accurately compare different film options. A higher-quality film may appear more expensive per roll, but, if it ensures fewer film breaks and requires fewer wraps, the overall cost per pallet may actually be lower.
INTRODUCING HIGH PERFORMANCE FILMS LIKE SHIELD
One immediate way to optimise cost per pallet is by switching to a high-performance film. Shield is a brand of specially engineered stretch film designed to deliver superior load stability at reduced film usage.
Key Advantages of Shield
Enhanced Stretchability Shield’s multi-layer construction offers high stretch levels, allowing operators to secure loads with fewer wraps. Fewer wraps per pallet means less film usage overall, resulting in lower costs per pallet.
Reduced Plastic Consumption Because it is engineered to do more with less, Shield can reduce plastic use by up to significant percentages when compared to standard films. This cuts down on the total amount of plastic being purchased, transported, and ultimately disposed of.
Stronger, More Reliable Wrap High-performance films like Shield resist punctures and tears better than their cheaper counterparts. A more reliable film cuts down on downtime and waste associated with re-wrapping.
Savings of up to 25% By lowering the amount of film needed per pallet and reducing damage or rework, organisations can see cost savings of up to 25% when making the switch from conventional pallet wrap.
THE PLASTIC PACKAGING TAX AND ITS IMPACT
What Is the Plastic Packaging Tax?
The UK’s Plastic Packaging Tax (PPT) applies a charge of £200 per tonne of plastic packaging that does not contain at least 30% recycled material. This tax aims to incentivise businesses to use more recycled content in their packaging and to reduce overall plastic waste.
How It Affects Pallet Wrap Costs
Any business that manufactures or imports plastic packaging (including stretch film) is potentially liable for this tax. Even if you’re purchasing film from a distributor, the costs incurred from PPT may be passed on to your organisation in the form of higher prices.
Increased Overheads If your pallet wrap doesn’t meet the 30% recycled content threshold, the extra charge can quickly add up for large-scale operations.
Hidden Costs Many businesses only discover the magnitude of PPT after noticing a sharp increase in their film costs. This additional expense can represent a sizeable hit to profit margins.
Mitigating the Effects of PPT
Switching to a high-performance film like Shield can help you manage PPT costs in two ways:
Reduced Total Film Usage Using less film overall means you’re effectively lowering the volume of taxable plastic.
Recycled Content Options Shield films can be manufactured to meet or exceed the 30% recycled content threshold, ensuring compliance and minimising the additional tax burden.
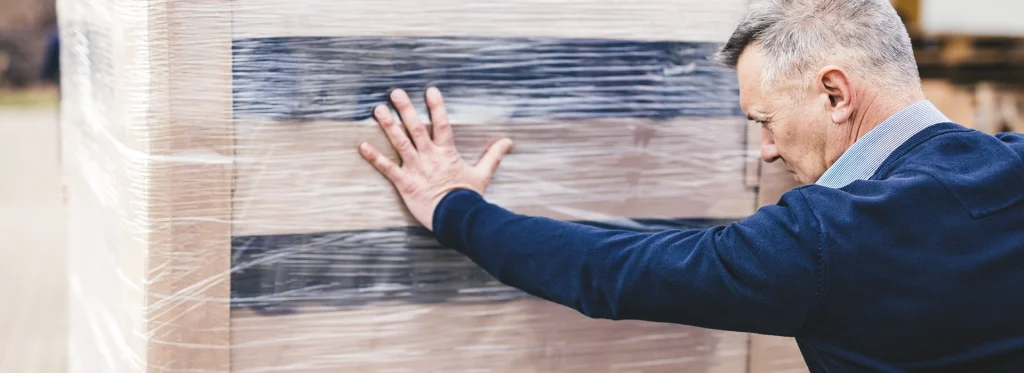
HIDDEN COSTS OF LOW QUALITY FILM
Low-quality films may seem appealing if you only look at the unit price. However, numerous hidden costs can surface:
Labour and Downtime Frequent breaks or tears lead to time lost in re-wrapping and machine adjustments. Over weeks or months, this can translate into significant overheads.
Damage in Transit If the film fails to properly secure your pallets, you risk product damage during transport. Damaged goods can result in product returns, refunds, and potential harm to your reputation.
Waste Disposal Extra layers of film and broken pieces create additional plastic waste. Not only does this have environmental implications, but it also adds to your disposal costs.
By weighing these hidden costs against the potentially higher per-roll price of a premium film, you often find that a more robust wrap yields better value.
OPTIMISING YOUR PALLET WRAPPING PROCESS
To ensure you’re getting the best results from any pallet wrap—whether you opt for Shield or another high-performance option—consider these steps:
Measure Your Current Cost per Pallet
Calculate how much film you use per pallet.
Factor in the cost of re-wrapping, downtime, and any plastic taxes or disposal fees.
Evaluate Machine Settings
Ensure your wrapping machines are calibrated for the chosen film, especially regarding tension settings and pre-stretch levels.
Proper calibration maximises film efficiency and minimises breakage.
Review Pallet Configurations
Place products neatly and evenly to prevent gaps that may cause wrap failure.
Check if anti-slip sheets or corner boards could further stabilise loads.
Train Your Staff
Proper training in stretch film application ensures consistent use and minimises error.
Clear guidelines or standard operating procedures help maintain uniformity across shifts.
Keep an eye on performance metrics and costs over time.
Conduct regular packaging audits to identify areas for improvement.
THE LONG TERM VALUE OF HIGH PERFORMANCE FILMS
While switching to a high-performance film such as Shield might carry a higher purchase price, the broader picture usually reveals lower overall costs per pallet. These savings stem from:
Lower Film Usage Fewer layers of film mean you’re using less plastic, saving money and cutting down on environmental impact.
Reduced Re-Wrapping A stronger film lowers the chance of tears, eliminating multiple wrap cycles per pallet.
Compliance with Regulations Meeting or exceeding the 30% recycled content threshold can help minimise exposure to the Plastic Packaging Tax.
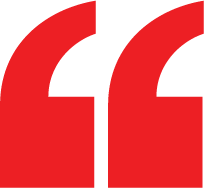

We often see teams zero in on the cheapest film per roll without realising how it drives up re-wrapping costs. Switching to a high-performance wrap doesn’t just save film—it cuts down labour time and slashes overall costs per pallet.

BEN THOMPSON
TECHNICAL MANAGER


CONCLUSION
Pallet wrap represents a critical, albeit frequently overlooked, factor in the total cost of packaging operations. Relying solely on cost per roll of film can be misleading and often leads to higher overall expenses due to waste, machine downtime, and product damage. By focusing on the cost per pallet and considering high-performance alternatives like Shield, you can reduce plastic usage, adhere to tax requirements, and ultimately save on total wrapping costs.
When selecting a stretch film for your business, remember to account for every cost—from the initial purchase price to the labour required for re-wrapping, potential product damage, and compliance with emerging environmental regulations. A thorough approach can yield both cost savings and greater sustainability, positioning your operation for long-term success in a competitive market.