
Back to blog
COMMON PALLET WRAPPING MISTAKES - AND HOW TO AVOID THEM
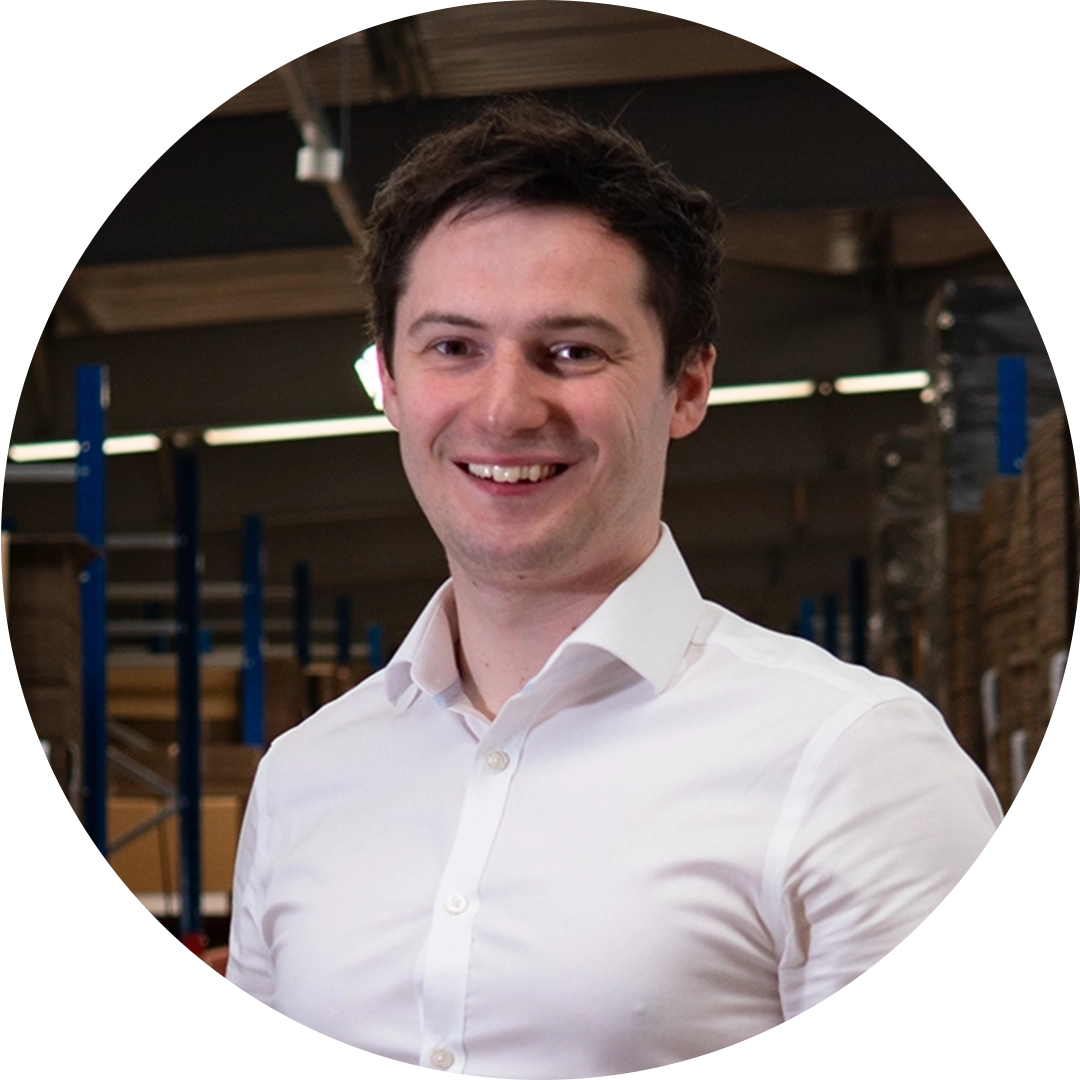
Written by
LIAM BLAND
Load Stability
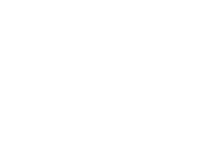
Table of Contents

Estimated read time: 23 mins
INTRODUCTION
Though it might seem like a straightforward process, pallet wrapping in certain instances certainly has a bit of a habit of being tricky to do the right way at times. Whether you’re overseeing operations on a busy warehouse floor or are responsible for sourcing stretch film, understanding the dos and don’ts of pallet wrapping can make a tremendous difference to your overall efficiency – not to mention your bottom line.
In this article, we’ll explore some of the most common mistakes made when wrapping pallets and offer you some practical tips on how to avoid them. By the end, you’ll have a clear sense of the key factors that influence pallet stability, how to choose the right film, and what steps you can take to improve consistency and cost-effectiveness.
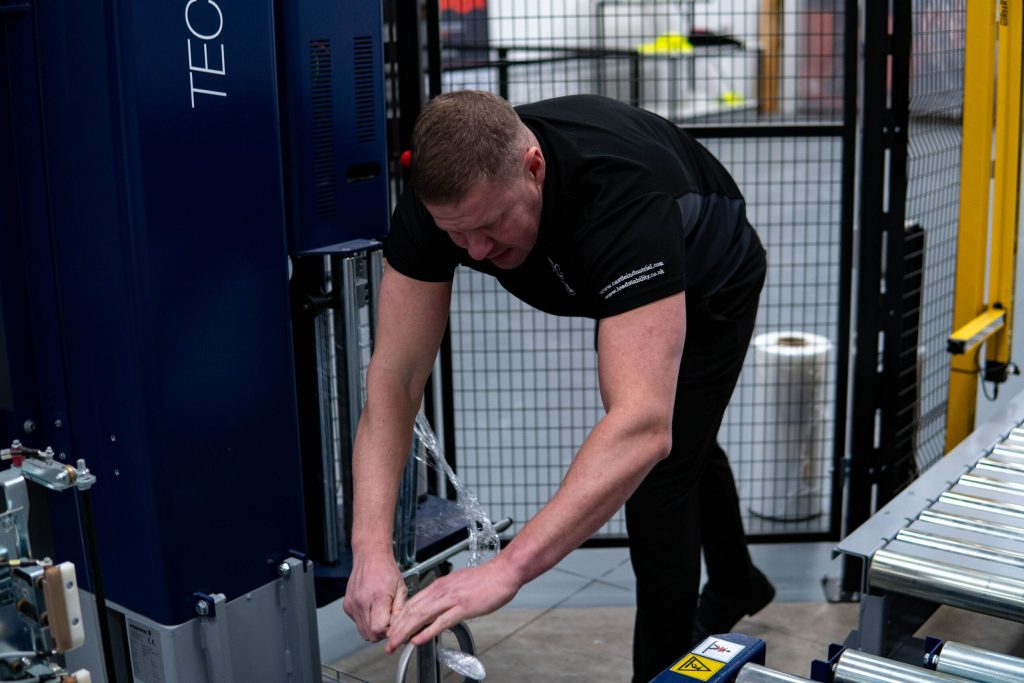
WHY PALLET WRAPPING MATTERS
The Real Impact on Load Stability
Pallet wrapping is more than just a final flourish at the shipping dock. It’s a critical step to ensure your products remain intact throughout handling, storage, and transit. When done correctly, good wrapping stops goods from shifting, toppling, or rubbing against one another – all of which can lead to damage.
Cost and Waste Reduction
Overusing film, or using the wrong type, often leads to unnecessary expense. On the flip side, under-wrapping can result in damaged goods, returns, and additional transport or handling costs. Striking the right balance saves money and reduces the amount of plastic waste your operation generates.
Safety and Reputation
A poorly wrapped pallet could collapse or shift during transport, creating hazards for drivers, warehouse staff, and anyone else who comes into contact with it. There’s also reputational risk: consistently delivering products that arrive in poor condition will erode customer confidence over time.
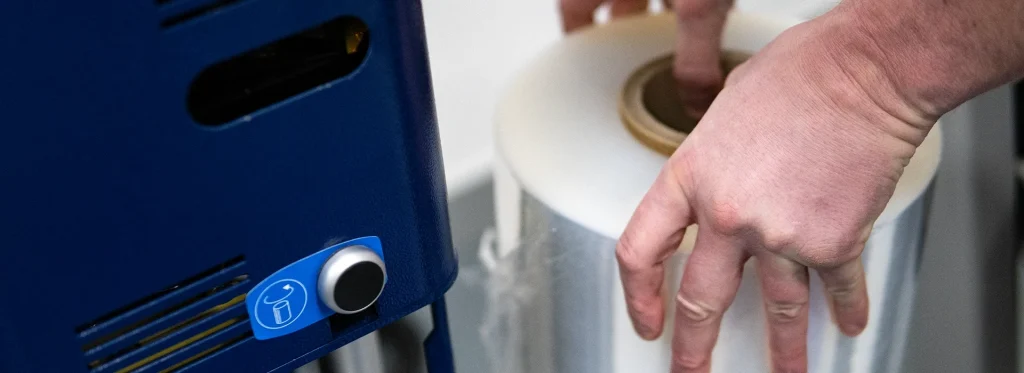
COMMON MISTAKES - AND HOW TO AVOID THEM
Choosing the Wrong Stretch Film
What Goes Wrong: Some companies treat stretch film selection as an afterthought. They might buy the cheapest film they can find or assume one type suits all loads. This approach often results in films that tear too easily, fail to properly stabilise the load, or require excessive wraps to secure everything.
Why It Hurts: Using the wrong film can drive up costs because you’ll likely need to use more of it, or you’ll face more damaged goods. If the film tears or doesn’t hold well, it can lead to higher waste levels too.
How to Avoid It:
Speak to an expert and be sure to test different types (e.g. varying gauges or thicknesses).
Consider the weight, shape, and fragility of your goods. Heavy or awkwardly shaped loads may need a stronger, puncture-resistant film.
Keep in mind that a more expensive film might offer greater stretch capacity, meaning you use less overall.
Insufficient or Inconsistent Film Tension
What Goes Wrong:
When wrapping is done by hand or by poorly calibrated machines, tension can vary wildly. Sometimes it’s too loose, leaving the load insufficiently secured. Other times it’s so tight that the film snaps or crushes delicate products.
Why It Hurts:
Under-tensioned loads are more prone to shifting and toppling. Over-tensioned film can damage packaging or even the goods themselves – especially if you’re shipping items like bottled drinks or fragile electronics.
How to Avoid It:
Calibrate any wrapping machines regularly, making sure the tension settings align with the type of film you’re using.
Train staff on the proper technique if they’re hand-wrapping pallets. If using machine wrap, ensure operators know how to adjust the settings for different product types.
Regularly inspect wrapped pallets and make adjustments as needed.
Failing to Secure the Pallet Base Properly
What Goes Wrong:
It’s surprisingly common for people to focus on wrapping the goods themselves, forgetting to incorporate the pallet base. The film might only lightly hug the edges of the pallet or skip it altogether.
Why It Hurts:
If the goods and the pallet aren’t effectively ‘locked’ together, the load can slide right off the pallet during transport or loading. This is a recipe for product damage and potential injury to staff.
How to Avoid It:
Start wrapping at the bottom, circling the pallet two or three times to ensure the film grips the base.
Make sure the first wrap is tight and extends under or around the corners of the pallet.
In cases where you’re dealing with heavier loads, adding extra wrap around the base can offer extra security.
Using an Inconsistent Wrapping Technique or Pattern
What Goes Wrong:
If different operators each have their own ‘style’, you can end up with wildly varying wrap patterns. Some might spiral quickly up the load; others might apply more layers at the top and neglect the middle.
Why It Hurts:
Inconsistent wrapping can leave weak spots, resulting in load instability. It can also make it difficult to diagnose problems when something goes wrong since each pallet might have a completely different wrap pattern.
How to Avoid It:
Standardise a wrap pattern within your team or facility. For instance, move from the bottom to the top, slightly overlapping each layer.
Incorporate a reinforcing wrap around the centre of tall pallets or other weak points.
Use visual guides or posters near the wrapping area to help staff follow the same procedure.
Overstretching or Understretching the Film
What Goes Wrong:
Sometimes operators will try to stretch the film beyond its recommended capacity to ‘save on plastic.’ In other cases, they’ll fail to stretch it enough because they’re not aware of the film’s capabilities.
Why It Hurts:
Overstretching can create weak, thin areas prone to tearing, while understretching may require more film wraps to secure the load properly. Either way, you’re not using the film to its full potential.
How to Avoid It:
Check the manufacturer’s guidelines on the optimal stretch percentage for your film. Different films have different elongation thresholds.
Perform test wraps to see how many rotations you need and measure how much the film stretches.
Consider using pre-stretched film or a machine that controls and measures stretch to remove some of the guesswork.
Ignoring Load Configuration
What Goes Wrong:
Not all loads are the same. Items with unusual shapes or distributions of weight need special care. Tall or top-heavy stacks might topple if wrapped using a one-size-fits-all method.
Why It Hurts:
Inconsistent or inappropriate wrapping can lead to unstable loads, product damage, and accidents. It can also mean you end up using more film than necessary.
How to Avoid It:
Evaluate each load’s shape, height, and weight distribution before deciding how to wrap.
Consider adding corner boards or top caps for particularly tricky loads.
Consult a packaging specialist if you regularly deal with complex or high-value goods.
Neglecting Machine Maintenance
What Goes Wrong:
Over time, essential parts of your wrapping machine can wear down – for instance, the rollers that stretch the film or the belts that drive the wrapping arm. Without regular maintenance, these small issues can become big problems.
Why It Hurts:
A poorly maintained machine will apply film inconsistently, waste film, or cause sudden breakdowns. This leads to downtime, higher maintenance costs, and subpar wrapping quality.
How to Avoid It:
Establish a maintenance schedule. Monthly or quarterly checks can extend equipment life significantly.
Keep basic spare parts on hand, like replacement rollers or belts, so minor issues can be fixed quickly.
Encourage operators to report odd noises or performance drops straight away.
Lack of Proper Training and Oversight
What Goes Wrong:
People sometimes assume wrapping pallets is simple enough that it doesn’t require formal instruction. While it’s not rocket science, it does need consistency and a solid understanding of best practices.
Why It Hurts:
Untrained staff may use incorrect techniques, resulting in wasted film, poor load stability, or even injury if they’re unaware of safe working distances around the machine.
How to Avoid It:
Provide structured training sessions for new and existing staff, covering both manual and machine operation.
Offer refresher courses or quick tests to ensure techniques remain consistent over time.
Encourage team leaders to spot-check how pallets are being wrapped and offer on-the-spot coaching.
Overlooking Environmental Factors
What Goes Wrong:
Temperature swings, high humidity, dust, and other environmental conditions can all affect how well your wrap adheres and how stable your loads remain. Many people neglect to adapt their wrapping approach to these changing conditions.
Why It Hurts:
Extreme cold can make certain films brittle, while high heat might cause them to stretch more easily. Moist or dusty environments can compromise the film’s grip, leading to slipping or weakening over time.
How to Avoid It:
Store your film rolls correctly: avoid areas with extreme temperature changes.
Consider films specially designed for cold or humid environments.
If your warehouse or transport conditions vary seasonally, re-evaluate your film choice or tension settings at different times of year.
PRACTICAL TIPS FOR BETTER WRAPPING
Conduct Regular Audits
Every so often, it’s worth taking a closer look at your wrapped pallets before they leave the warehouse. Do they feel stable? Are there any noticeable tears or loose areas? Small spot checks can prevent big headaches further down the line.
Use Technology to Your Advantage
If your volume justifies the cost, automated or semi-automated wrapping systems can ensure consistent tension and application. Some advanced machines even measure exactly how much film is used per pallet, helping you track costs.
Collaborate with Suppliers
Don’t be afraid to tap into your stretch film supplier’s expertise. They often have technical teams or consultants who can help you choose the right film for each application or troubleshoot persistent issues.
Track Performance
Whether you keep a simple spreadsheet or use a more sophisticated warehouse management system, tracking film usage, damage claims, and returns can reveal patterns and areas for improvement.
Standardise and Document
Create a brief but clear standard operating procedure (SOP) that outlines film type, tension settings, wrapping patterns, and any additional steps needed. Place a copy at the wrapping station for quick reference.
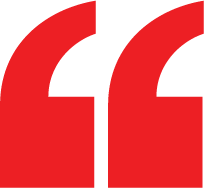

A properly wrapped pallet is the backbone of any stable supply chain. It’s all about finding that sweet spot between enough tension to secure the load and not going overboard. If you strike that balance, you’ll save money on film and cut down on damaged goods in one go.
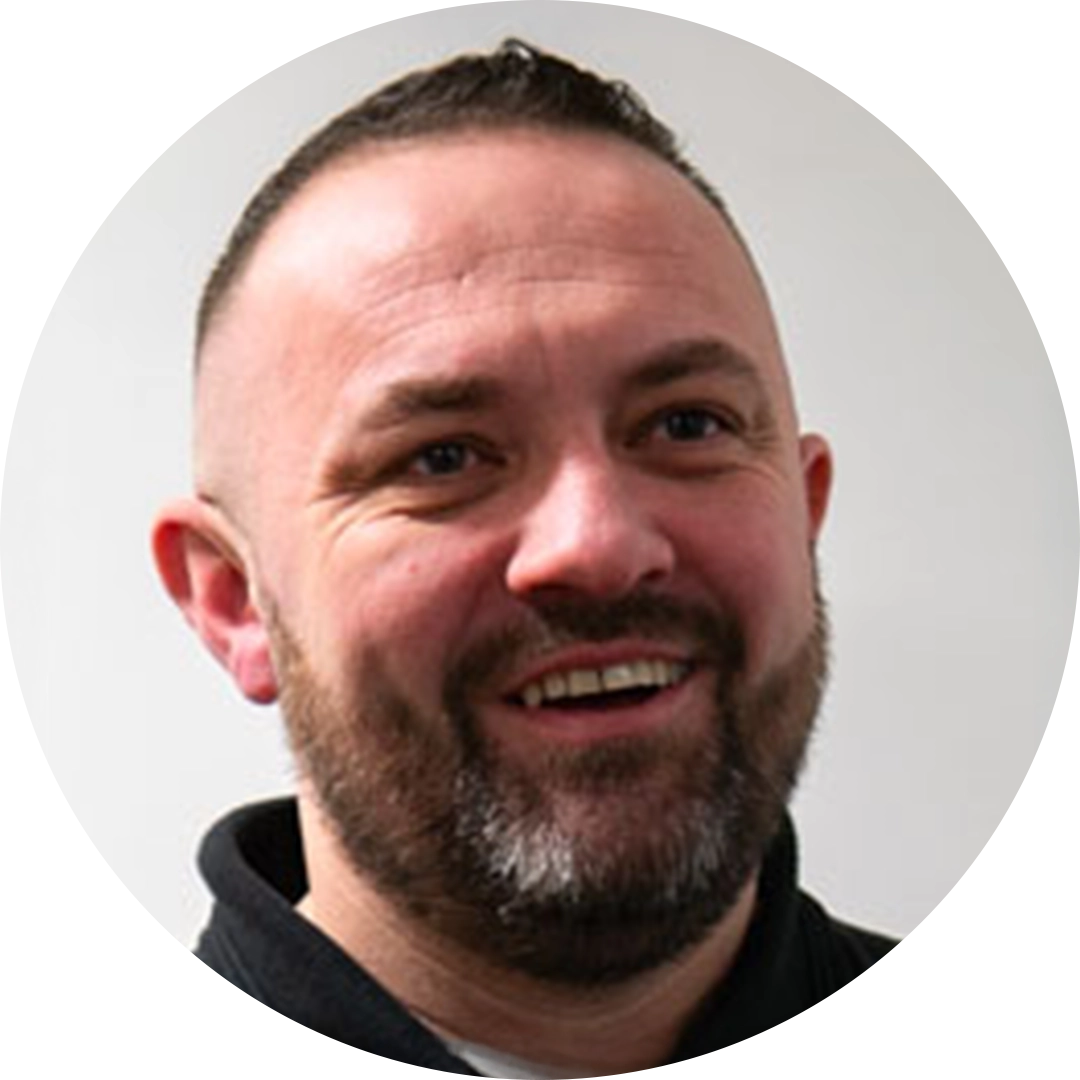
MARTIN COLLINS
LOAD STABILITY SPECIALIST


CONCLUSION
A little attention to detail goes a long way in the world of pallet wrapping. From selecting the right film to ensuring a consistent wrapping technique, each step plays a part in delivering products safely and efficiently. By avoiding the common mistakes listed above, you can maintain stronger load stability, reduce waste, and keep your supply chain running smoothly.
Whether you’re managing a sprawling distribution centre or a modest warehouse, the principles remain the same: consistency, correct equipment, and well-trained staff are the cornerstones of effective pallet wrapping. If you haven’t done so already, consider reviewing your current practices and reach out to knowledgeable suppliers for advice. You might be surprised how small adjustments in wrapping can make a big difference to your overall operational performance.