More than a year into the planning and execution of the project, we’re thrilled to launch our state-of-the-art testing centre at Oakwood Way in Carnforth, Lancashire. This facility promises to be a game changer for professionals that want to ensure they’re optimising both their palletising and packaging processes.
Providing customers with real time data and in-depth analysis, previously unavailable at the scale we’re now able to offer, this facility is now considered to be the UK’s most comprehensive for load stability.
In today’s fast paced logistics landscape, this kind of intelligence is invaluable and it’s our hope that this investment will allow businesses across the country to boost efficiency, reduce costs and enhance safety throughout the supply chain.
Why Load Stability Matters…
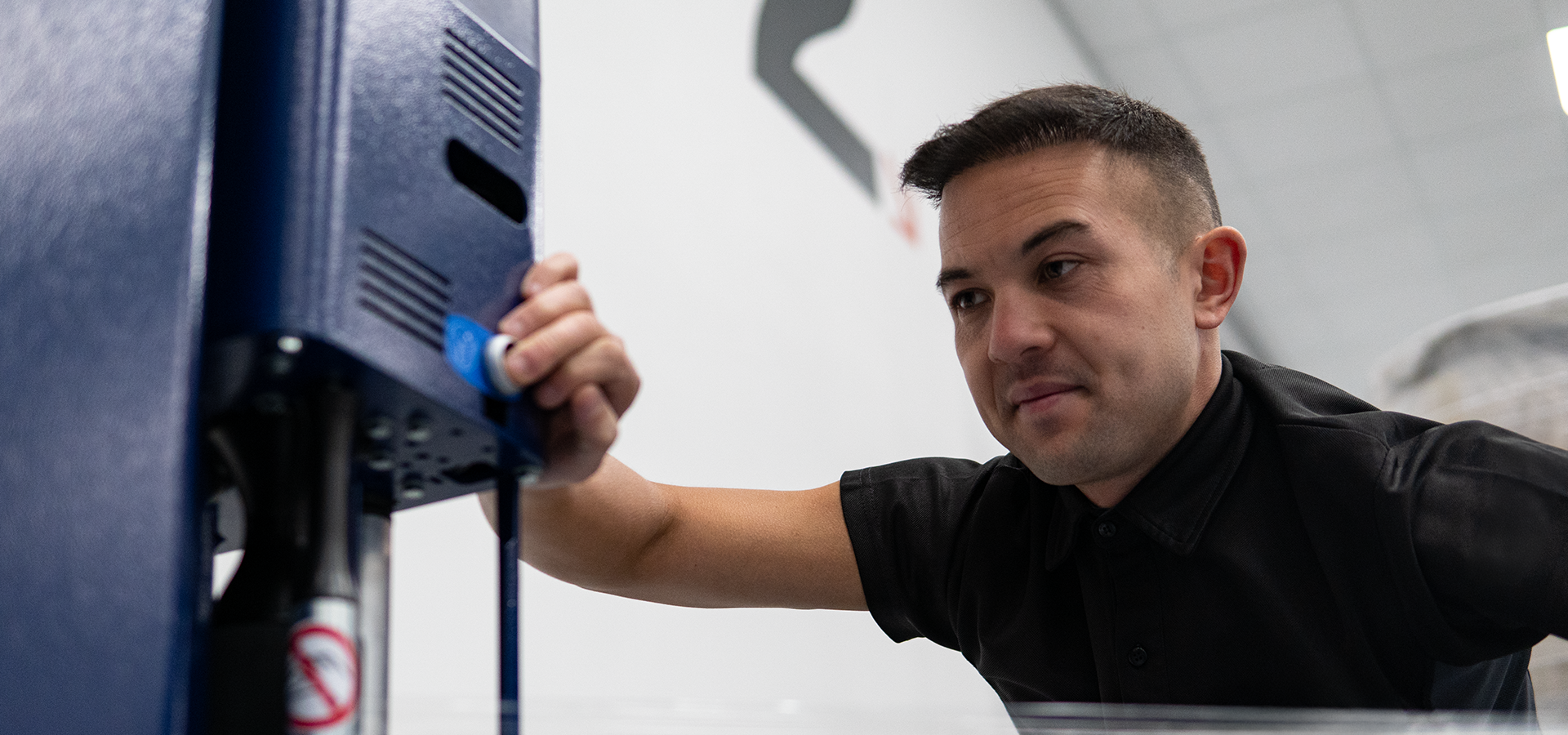
Before diving into the exciting details of our new facility, let us provide a little more context on the importance of load stability – and why it’s such a crucial factor in modern logistics and packaging.
Poor load stability can lead to a host of issues, from destabilising the supply chain to long lasting reputational damage, so if you’re in the business of transporting goods, mitigating these potential disasters are paramount to the smooth running of ops. Ensuring your pallets are securely wrapped and stable will prevent goods from moving in transit, or worse, collapsing.
At our new load stability testing centre, we now have the capability to address existing problems or concerns with cutting edge tech and importantly, the data to back our knowledge and experience.
Welcome to the Future of Load Stability Testing
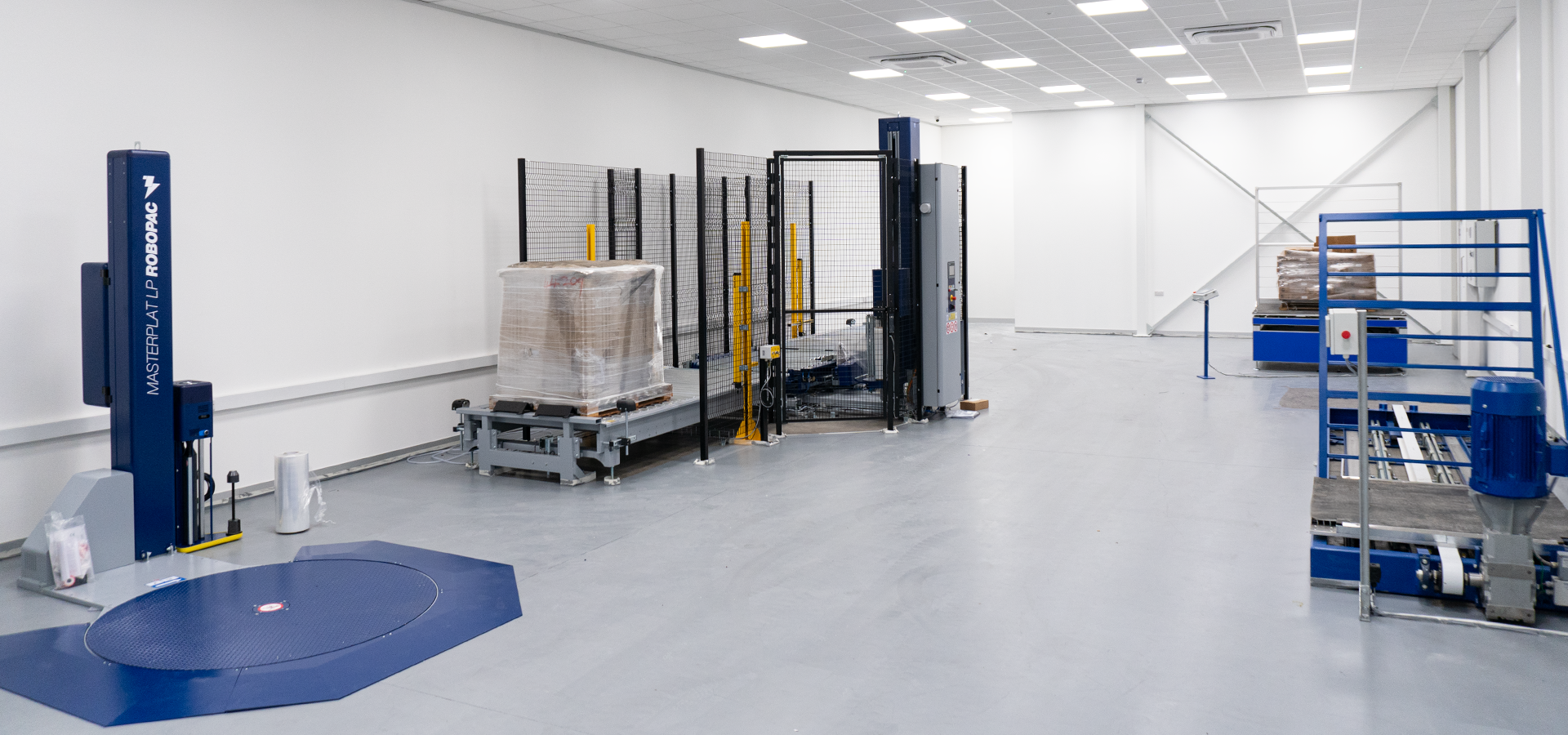
More than the addition of testing equipment to our arsenal, the testing centre provides customers with a priceless opportunity to learn more about their processes and get closer than ever before to ultimate load stability.
With a leading collection of testing machinery, the controlled environment allows us to provide pinpoint analysis and real time feedback on your processes, so that you can leave confident your goods are road safe and fully optimised.
Let’s take a look at some of the key machinery and testing capabilities that make our centre unique…
Cutting-Edge Technology: A Glimpse Into Our Machinery
Tilt Vibration Bench
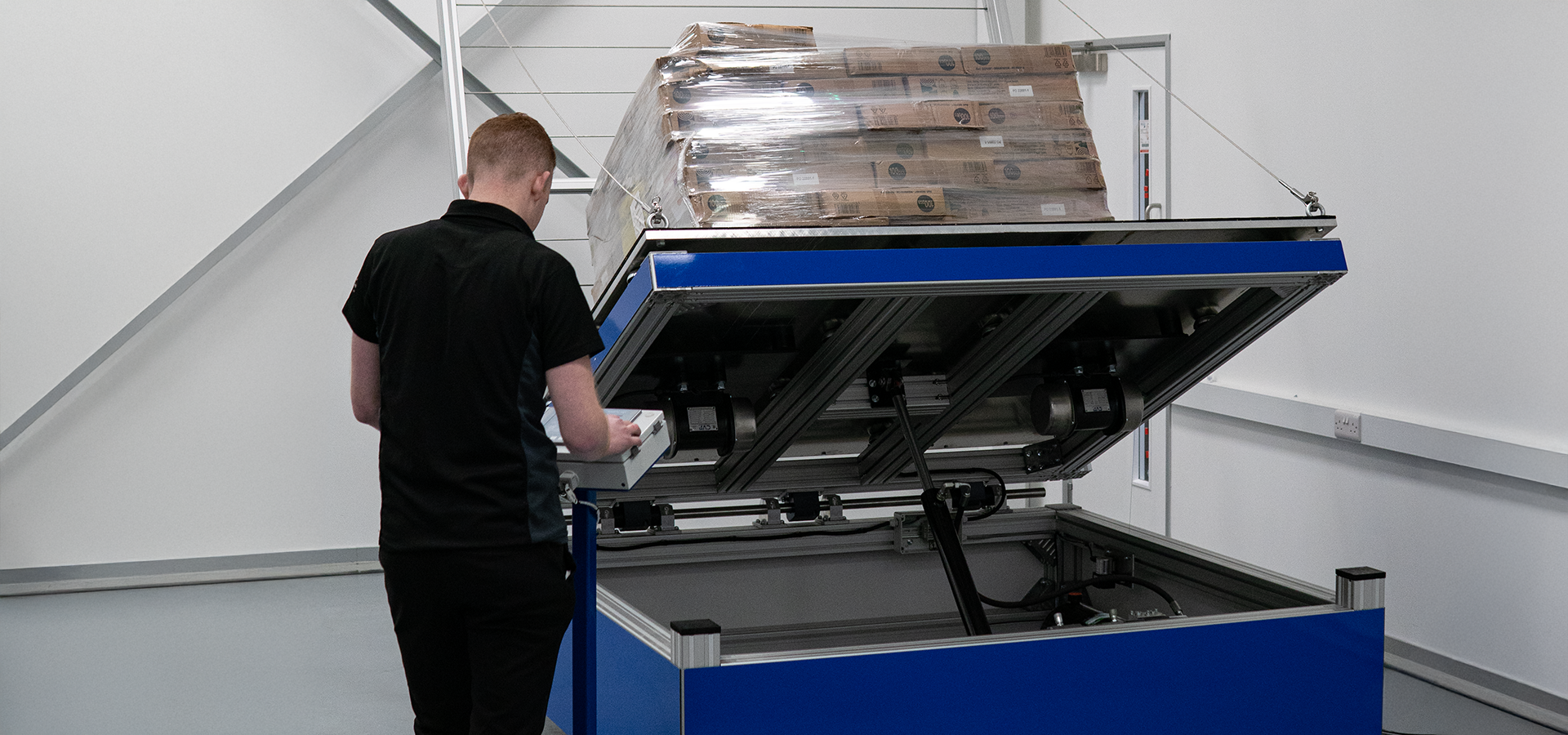
One of the standout features of our testing centre, the tilt vibration bench, offers unique insight into how a pallet performs against steep gradients and the rigours of damaged roads.
Comprised of the bench itself, and a specialised Basler 3D camera, this test can be used to assess the integrity of your wrapping material, and even the slightest movements of goods on your pallet. This is an essential tool for assessing palletisation techniques and the overall efficacy of your wrap.
For businesses wanting to meet ISTA standards, the tilt vibration bench provides the results necessary to see if your cargo meets their standards.
Acceleration Bench
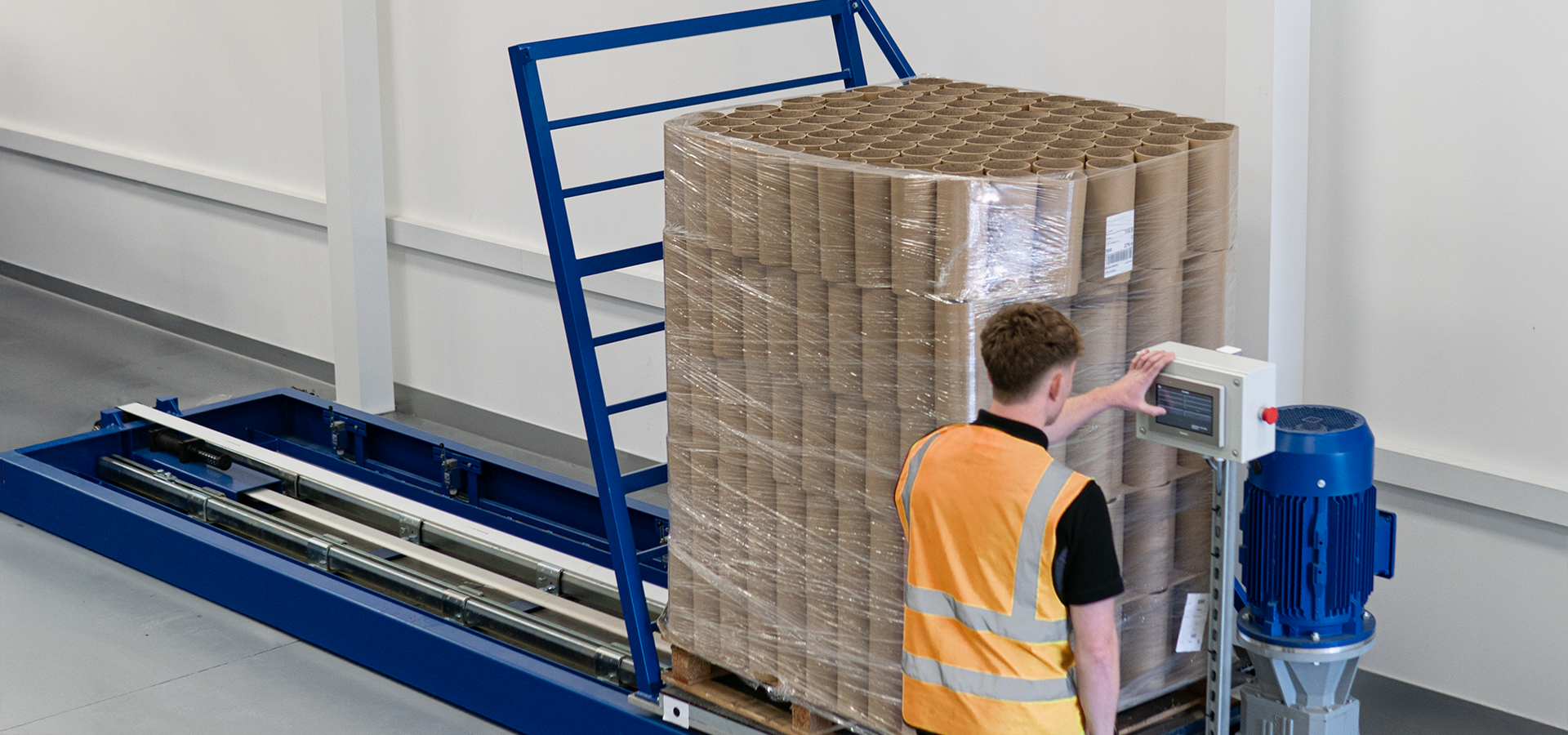
Designed to simulate the effects of sudden braking, the acceleration bench allows us to replicate g-force of up to 0.8g in a controlled environment – which means we can test your pallets against the EUMOS 40509 standard.
Working as follows, this test includes another cutting-edge camera. This time trained to specific tracking points on your cargo and provides super slow-motion footage we use to analyse the pallet redistribution post-test. It’s vital information for those serious about optimisation, because it offers real time feedback on how your freight performs under what is common duress in transit.
As mentioned earlier, the test provides businesses with the opportunity to see how their current pallets perform against the EUMOS 40509 standard. More of which you can learn about at the link here.
Automated Pallet Wrapping Line
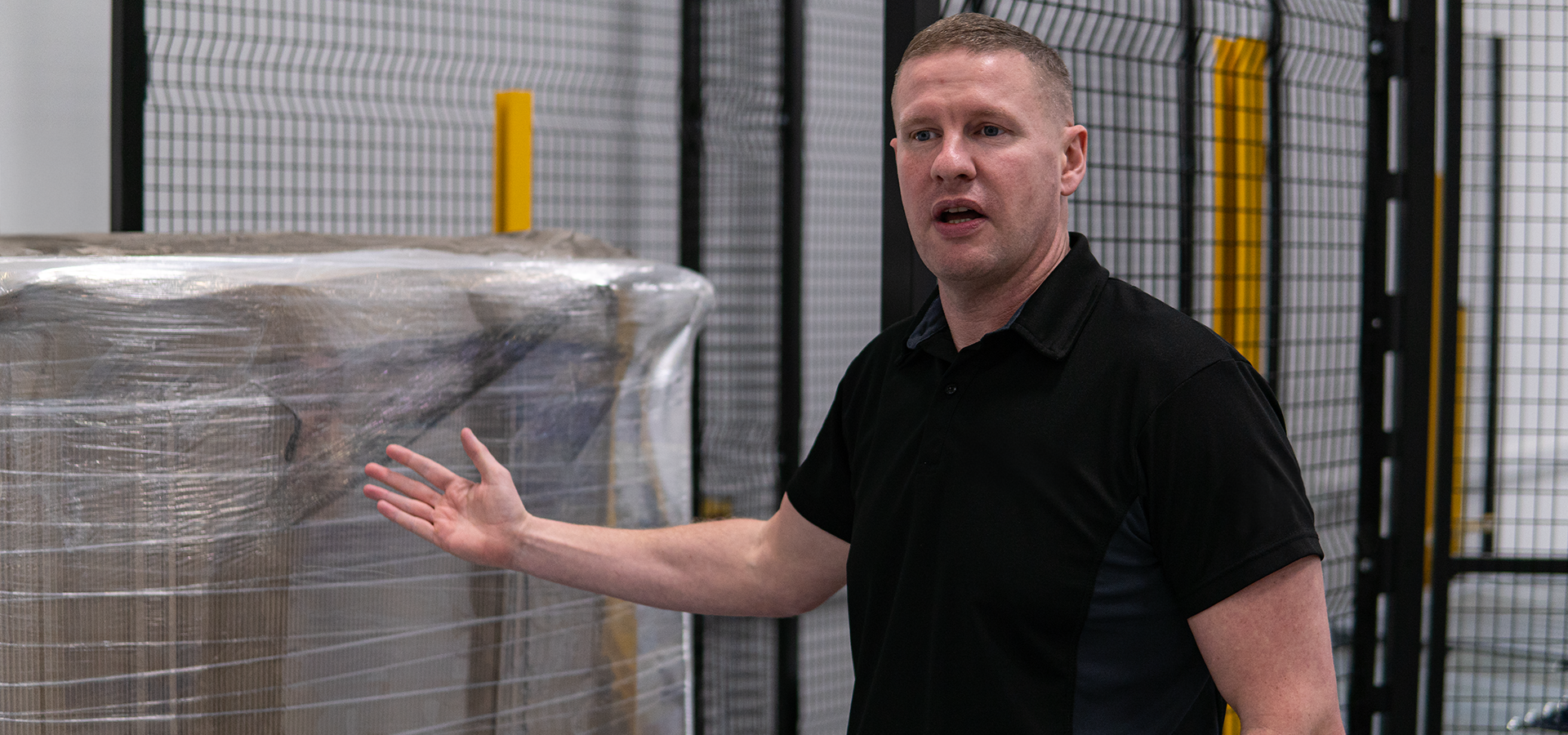
Designed with purpose to work a variety of load types, our fully automated wrapping line provides the answer to inconsistencies in wrapping. The Technoplat 3000 eliminates human error and provides optimised wrap usage to ensure goods are secured with the ideal amount for maximum efficiency and efficacy.
By testing your pallets with this machine, you’ll instantly be able to see the potential for reducing material waste and how you could streamline operations for huge cost savings – not to mention, improvements to your load stability.
S7 Robot Wrapper
If you’re looking to increase the efficiency of your operations, then few tools can be as effective for wrapping complex goods as the S7 robot wrapper. Similar to the automated line, this popular piece of tech is capable of providing consistent wraps without sacrificing stability.
On display at our testing centre, customers can choose to test this innovative solution so that they can understand how embracing automated tech can further their processes.
Low Profile Turntable Wrapper
Making it possible to load from any angle, the low profile of our Masterplat Plus provides customers with a versatile turntable that can perform to industry leading standards.
With a fixed stretch of 250%, though alternate gears can be purchased, this machine allows us to showcase the benefits of a consistent wrapper with a stellar reputation for its reliability.
Why Our Centre Stands Out: Unparalleled in the UK
While other companies offer load stability testing, few can match the ambition and breadth our new facility provides. With some of the industry’s most innovative machinery, combined with our expert knowledge and experience, we can now offer unparalleled detail on your operations in real time.
And at our centre, you won’t just get a standard report—we’re providing customers with an experience. A series of visual experiments so that you can get a comprehensive understanding of where the strengths and weaknesses of your operations lie.
If you want to truly understand how your goods perform in transit, and how close you are to ultimate load stability, then booking a visit is a must.
Start your conversation with a specialist by visiting us here.